Energy efficiency is no longer the buzzword it used to be in today's manufacturing landscape. Instead, it is a transformative force that can significantly enhance operational performance, reduce costs, and contribute to sustainability. With rising energy costs and increasing environmental scrutiny, the imperative to adopt energy-efficient practices has never been more pressing.
Improving a company's energy efficiency can lead to substantial cost savings. Energy management systems enable manufacturers to track and manage energy so that areas where cost savings can be found without a lot of capital investment are identified.
Case Study: LED Lighting
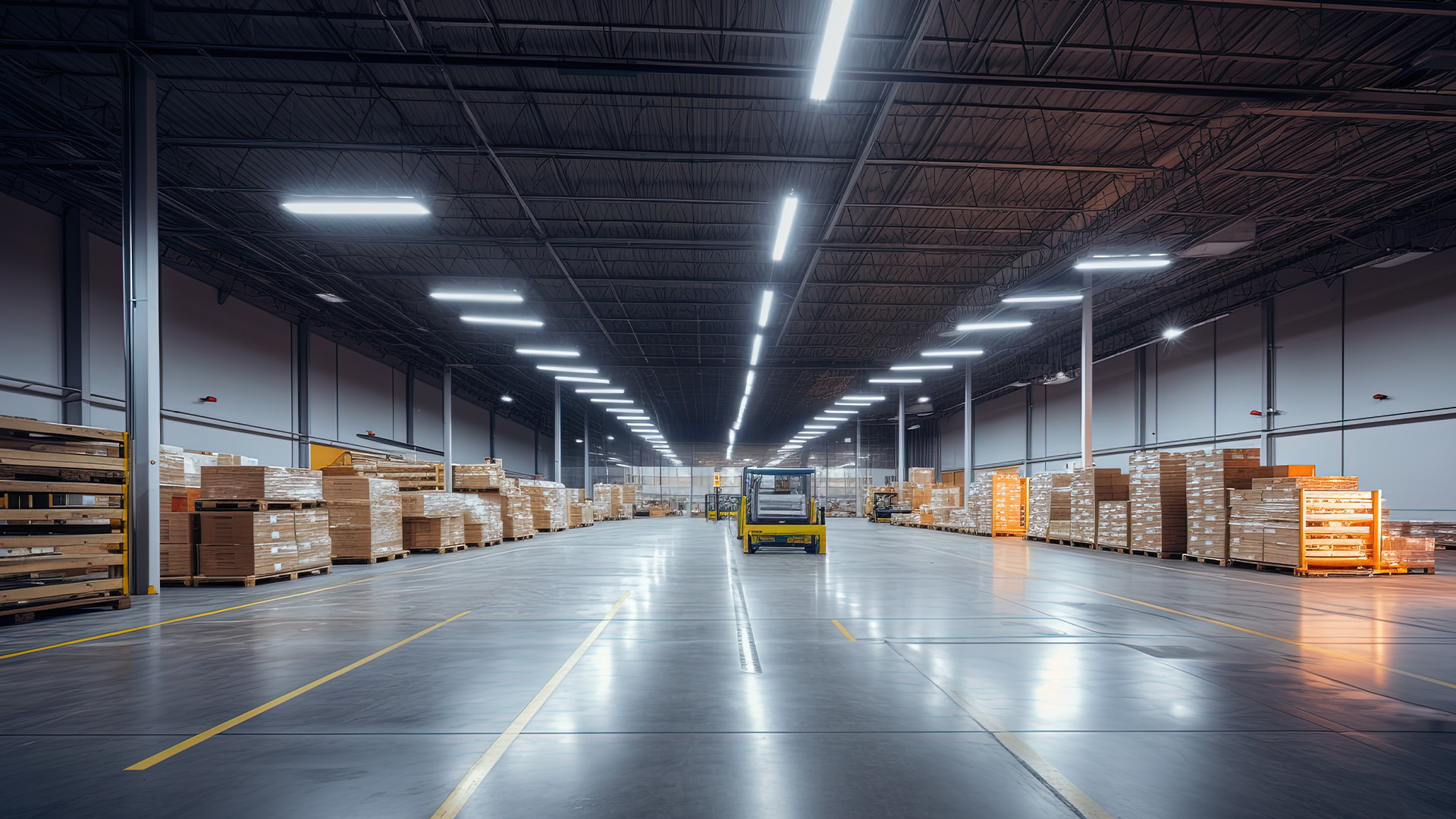
The most accessible and practical measure to save energy is the replacement of incandescent bulbs with LEDs. While their lack of efficiency has long led to widespread condemnation of incandescent bulbs for burning a significant portion of the energy consumed without emitting corresponding visible light, LEDs use much less electricity to illuminate.
As pointed out by the U.S. Department of Energy, LED bulbs use up to 90% less energy than the traditional incandescent bulb and can last as long as 25 times longer. Manufacturers can save thousands of dollars annually on their electricity bills by replacing only a few hundred bulbs in a factory setting.
Energy Audits
Another critical activity in quick wins is conducting regular energy audits. Energy audits are practical tools for identifying what a company is doing inefficiently and where improvement areas lie. An energy audit's comprehensive process moves through every one of the systems used in the facility that consume energy, ranging from HVAC systems to lighting and machinery. The report generated by an energy audit states energy-saving opportunities and cost-effective improvements to implement immediately. For example, research by the National Institute of Standards and Technology suggested that energy audits can help a plant save between 10% and 30%, depending on the prevailing conditions at each facility. Implementing recommendations from an energy audit allows manufacturer companies to reap substantial reductions in energy consumption overnight.
Environmental Benefits
Some of the ways to reduce carbon dioxide emissions include improving energy efficiency, as well as cost savings. Energy consumption is usually coupled with production processes. With companies utilizing high-performance technologies and practices, energy efficiency automatically improves, thus reducing their emissions.
Case Study: Energy-Efficient Motors
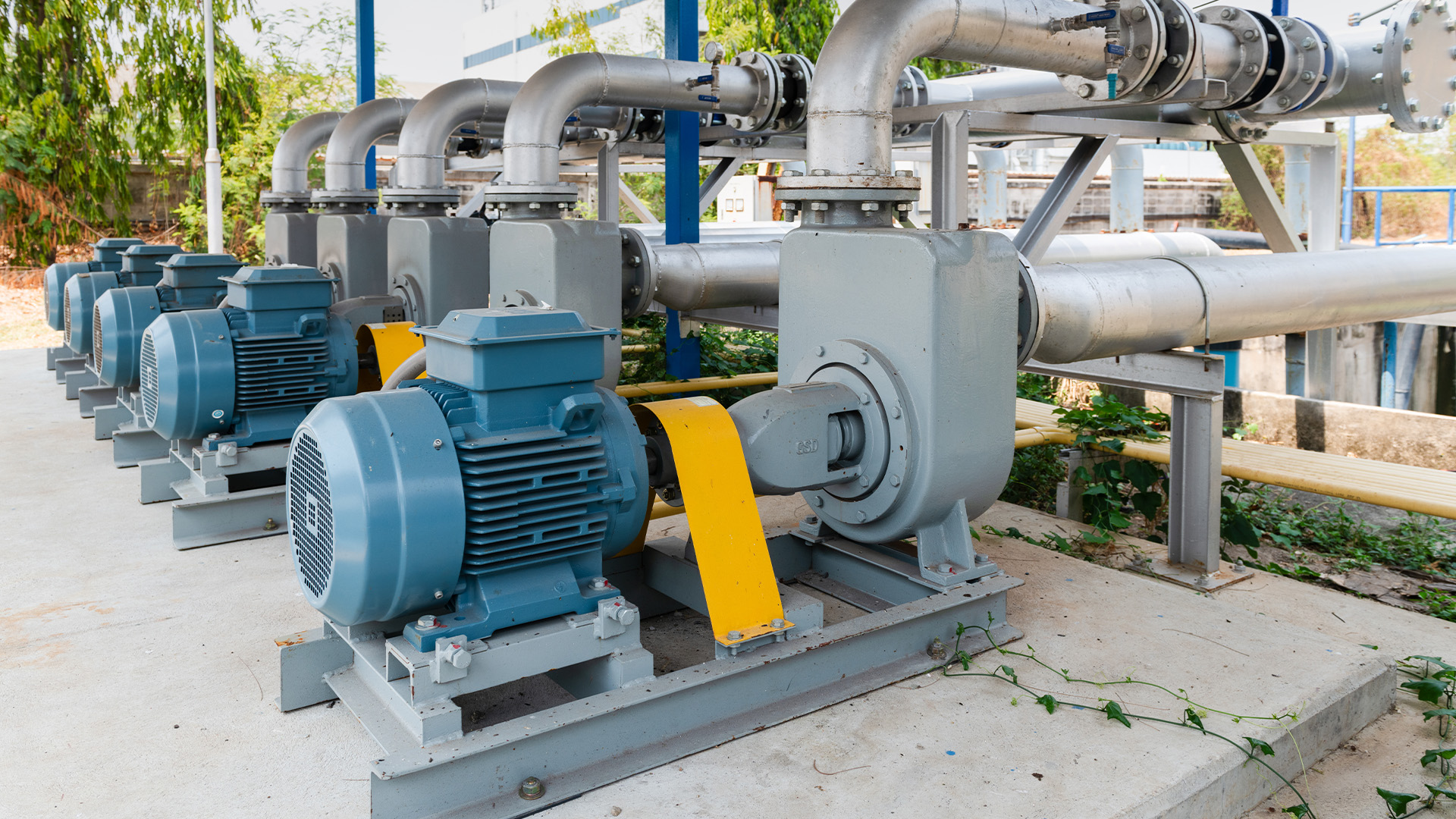
Considerable environmental benefits will be obtained from energy-efficient motors because conventional motors are inefficient. Though admittedly wasting a significant proportion of the electrical energy consumed in valuable work, energy-efficient motors harness advanced technologies, like permanent magnet designs or variable speed drives, to reduce energy consumption while enhancing or preserving performance.
According to the U.S. Department of Energy, replacing traditional motors with energy-efficient ones can save 10% to 50% of energy usage, depending on the application. Manufacturers enjoy saving energy costs while helping create a sustainable future by reducing carbon emissions.
Quick wins for immediate impact
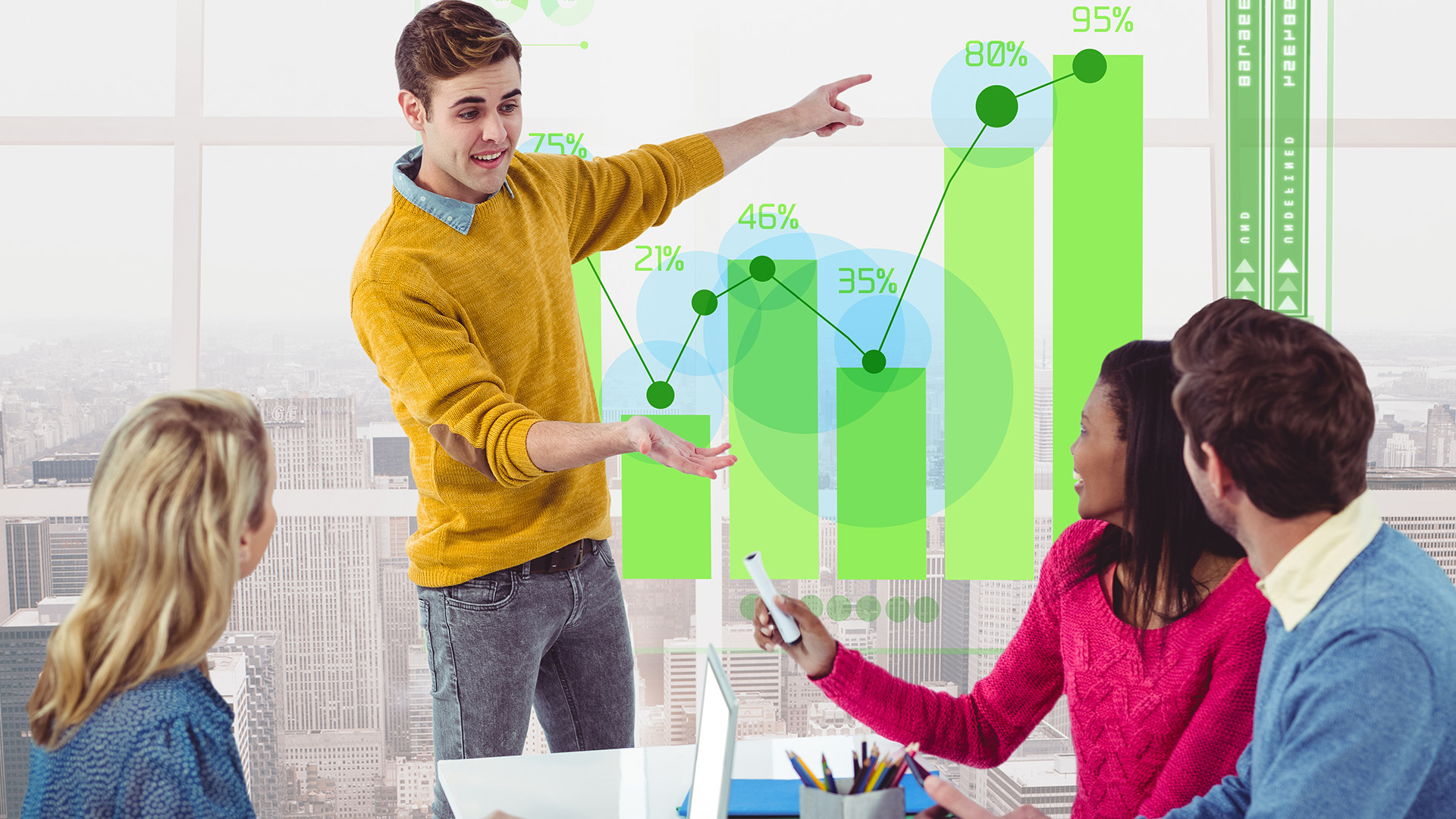
Energy Audits
Regular audits can identify inefficiencies in current operations and mark improvement areas. Manufacturers can immediately identify where savings can be made, using an energy audit to spot the locations and implement cost-effective measures.
Optimizing Production Schedules
Rescheduling the operating time of machines to reduce idle times helps save a lot of energy. For instance, a machine may be needed for a few hours in a day but continue running continuously. Adjusting it reduces much energy.
Employee Engagement
Employees should be motivated to save energy—such as switching off equipment when not in use. This fosters an efficient culture at work and the company at large. Sustainable practices among employees lead to saving energy, though it also offers a thrust in employee morale and productivity through engagement programs.
Investing in Smart Technologies
Smart manufacturing technologies would also bring real-time data on energy consumption and how to optimize operations. Such technologies include highly advanced sensors and monitoring systems that monitor real-time energy consumption.
Building a Sustainable Workforce
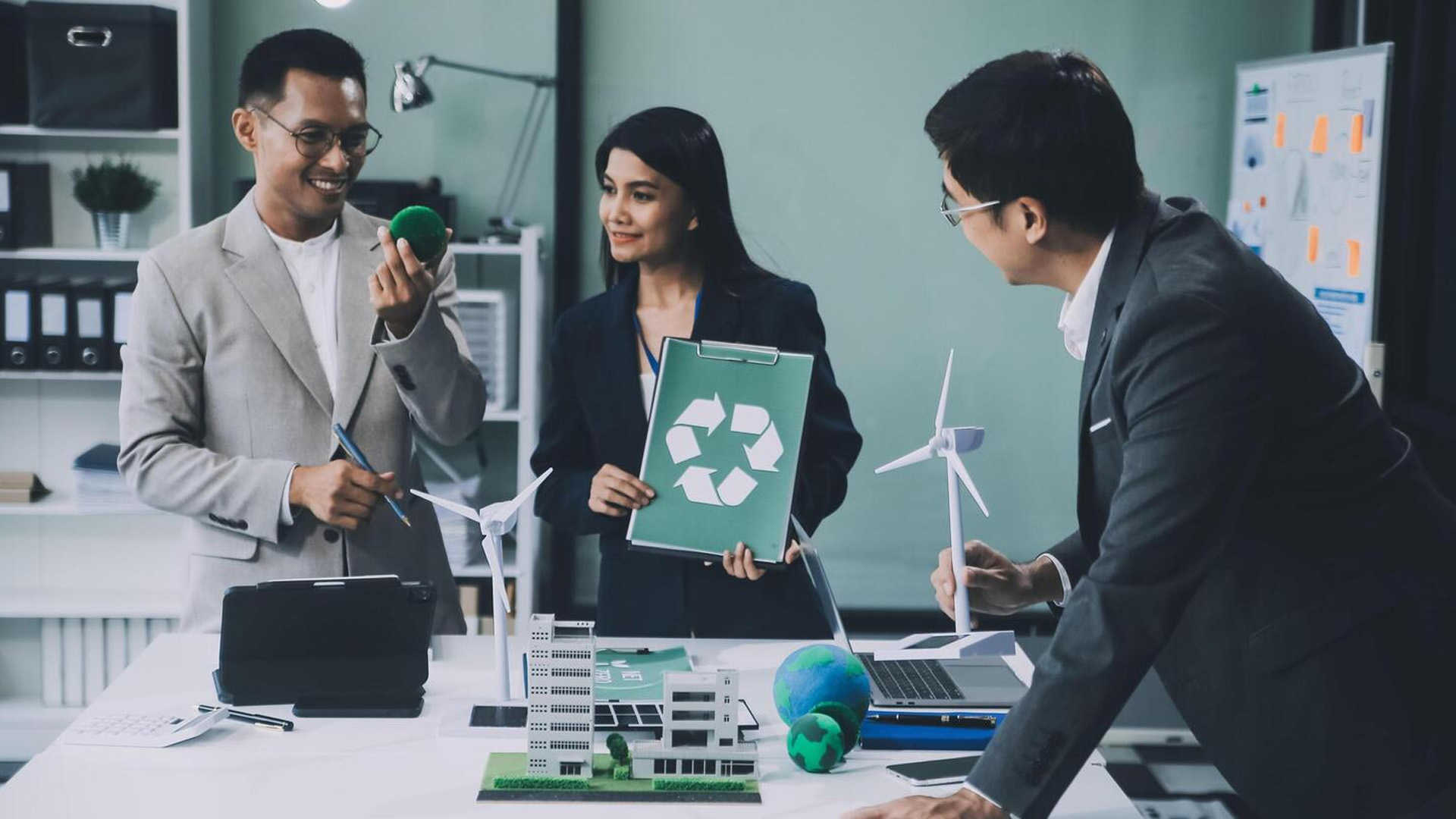
There also remains a great need to upskill the workforce in energy efficiency-related needs as manufacturers embrace this trend. Workforce development investment is indispensable for sustained improvements in energy efficiency and competitiveness of companies in the changing market.
Training Programs
These include classes on energy management systems, renewable energy sources, and sustainable practices. By investing their employees in such training, companies can ensure it is appropriately implemented and maintained. For example, the National Renewable Energy Laboratory (NREL) offers training programs designed to enhance skills among the manufacturing workforce on renewable energy and energy efficiency issues.
Collaboration for Success
Finally, partnerships with experts and industry players hastened the pace of realizing efficiencies in energy. Through external knowledge and resources, manufacturers can enforce best practices more efficiently, which, for the most part, may be tough when handling issues on funding opportunities and incentives offered through government programs. Moreover, the partnerships can be instrumental in providing immense support as companies strive to realize their sustainability goals while at the same time maximizing their operational efficiencies.
Industry Partnerships
Industrial collaborations are crucial for innovation and the adoption of energy-efficient technologies. With government agencies, one would have a shortcut to some funding opportunities and incentives created especially to favor energy-efficient initiatives.
The Green Leap Program, supported by the US Department of Energy, supports a great example through the American Made Challenge, which is about collaborative leverage toward energy efficiency in manufacturing. The program connects manufacturers with resources, incentives, and experts toward achieving sustainability goals. Initiatives like these provide manufacturers access to professionals with extensive experience implementing energy-efficient solutions.